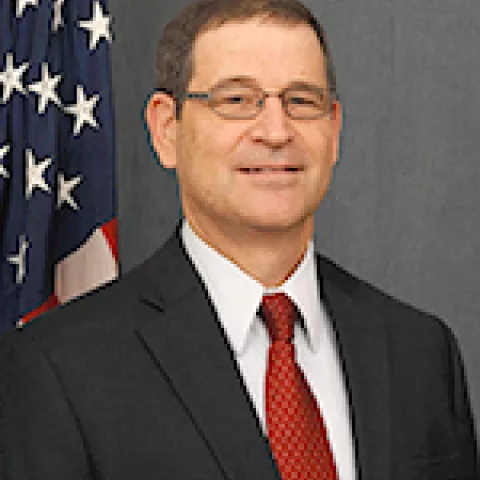
You are viewing ARCHIVED content published online before Jan. 20, 2025. Please note that this content is NOT UPDATED, and links may not work. Additionally, any previously issued diversity, equity, inclusion or gender-related guidance on this webpage should be considered rescinded. For current information, visit News Items | Bureau of Safety and Environmental Enforcement.
As audiences around the world watched the movie “Deepwater Horizon,” many of us found ourselves reflecting on the lessons of the actual tragedy that occurred April 20, 2010. Like most of you, I expected the movie to alter some of what the thorough investigations discovered, and I suppose the movie’s effort to create a “bad guy” was predictable. That said, those of us who work to reduce risks related to offshore drilling and upstream production know that it is simplistic and naive to tie offshore safety to “bad guys.” Only an industry’s cultural commitment to continuously improve safety will produce the type of decision-making that reduces offshore risks.
One contemporary example that illustrates the need to advance offshore safety culture can be found in the form of subsea connector failures. Connectors - typically studs, fasteners, and bolts - hold together critical subsea safety equipment, including blowout preventers. As long ago as 2003 there were indications that the offshore oil and gas industry was experiencing what we have come to call “the bolt problem.” In simplest terms, large bolts and other connectors have been prematurely failing in ways that could lead to catastrophic incidents.
The Bureau of Safety and Environmental Enforcement (BSEE) was created the year after the Deepwater Horizon tragedy so that a single entity could vigorously enforce regulations pertaining to safety, the environment, and resource conservation of the US outer continental Shelf. We became aware of the bolt problem in late 2012, when bolt failures caused the drillship Discover India’s lower marine riser package to become separated from the blowout preventer (BOP) stack. As a result, more than 400 bbl of synthetic-based drilling fluids spilled into the Gulf of Mexico, tripping a reporting requirement for the operator. BSEE’s investigation into that incident concluded that hydrogen-induced stress corrosion cracking due to hydrogen embrittlement led to the failure of numerous bolts.
In light of the Discover India investigation and other bolt failures that have since been discovered, we issued a nationwide safety alert. Fortunately, the failed bolts that we know about have not resulted in human or environmental catastrophes. In some instances, however, the potential for a serious result was evident. As of today, luck has been on our side.
I believe the bolt problem gives us a real chance to put the post-Deepwater Horizon reform mentality into practice. As such, BSEE has taken a number of steps that address the bolt issue, including:
- Changing reporting requirements for safety-critical equipment, including bolt failures. The Well Control Rule, which went into effect July 28, now mandates reporting of safety equipment failures in order to address potential systemic problems in their early stages. This change will allow us to build better databases and help us quantitatively understand how often failures occur
- Establishing the federal Interagency Bolt Action Team. This group of specialists, drawn from 20 agencies and bureaus, will collaborate to help BSEE identify the causes of bolt failures and to determine if the bolt failures impact safety for other industries
- Working with the American Petroleum Institute’s bolting work group, which is focused on BOP bolting issues
- Creating, through our confidential SafeOCS near-miss reporting system, a method for equipment failures to be anonymously reported by companies, contractors, and offshore workers
- Funding research by the National Academy of Sciences, Lawrence Berkeley National Laboratory, and NASA that will investigate how and why bolts fail.
There are already some encouraging signs that we can get ahead of the bolt problem. One example that supports my optimism can be found in a recall that General Electric issued. When the company learned that some bolts were failing on equipment they produced, it did the right thing and issued a global recall. That type of proactive behavior is evidence of a safety culture.
Although we cannot anticipate every problem, we can get ahead of problems quickly when the companies that make up an industry maintain strong safety cultures. A robust safety culture ensures that all other considerations are viewed through the lens of safety. Safety, in essence, is woven into the company’s business culture. Companies with such a culture greet the bolt problem with alarm, not skepticism. They move quickly to identify mechanisms that can help everyone find out the truth. They demand action and see their long-term financial health as directly tied to safe operations. I believe that is wise. Both individual operators, and the offshore energy industry as a whole, are morally and financially rewarded when they embrace a culture of safety.
The bolt problem is in front of us right now. Original equipment manufacturers, bolt manufacturers, and the dozens of companies using their equipment can demonstrate their safety cultures by working with the different groups who are trying to solve this issue. They can lean forward by acknowledging that a problem exists and more actively participating in the problem-solving process. Alternatively, displays of complacency and resistance demonstrate the absence of a safety culture. Companies that adopt such a high-risk approach are rolling the dice, and sending the wrong signal to the public, regulators, and their own investors. Our hope is that leaders across the offshore energy industry will step forward, as some already have, and espouse the virtues of an offshore safety culture while specifically using the bolt problem to demonstrate their commitment. That action would be an applauded around the world.
Brian Salerno
Director
Bureau of Safety and Environmental Enforcement